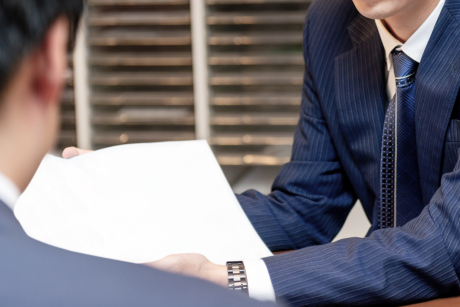
チョコ停が多く予定通りの生産が出来ない
自動車部品メーカー
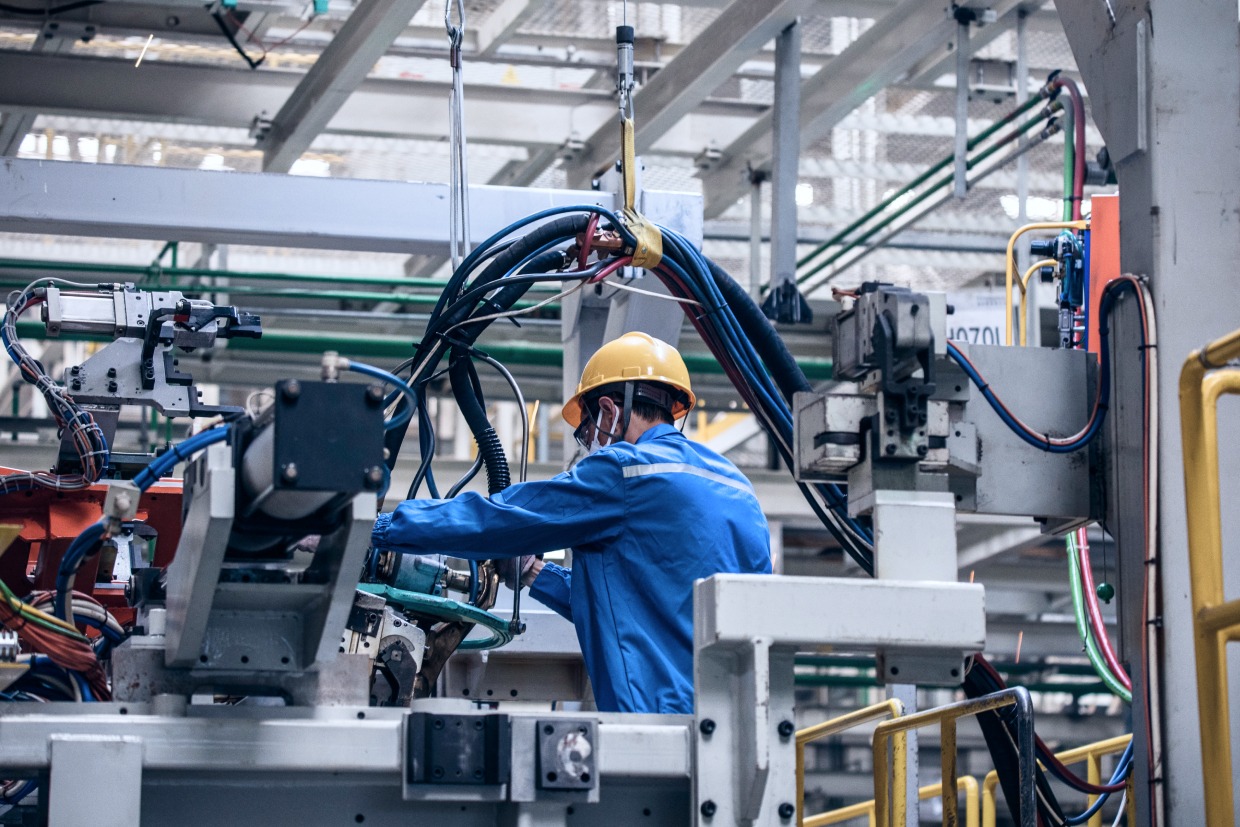
背景・課題
取引が浅く、関係性を構築するプロセスにあった企業から、チョコ停について相談を受けた。新たに設備を導入したものの、トラブルの多さと想定よりも生産性の向上が認められない点に課題を抱えていた。
設備のチョコ停は、他のラインでも頻繁に発生している。
- 生産が遅れ、サイクルタイムが合致しない
- 設備や製造が一時的に停止・空転する現象(チョコ停)が頻発
- 自社内に保全専門部署がない
提案/課題解決
TOKIWA営業マンの初動対応で問題解決。改善課題も明確になる。
生産現場の経験がある営業スタッフが担当。現場に直接足を運び、改善箇所とスケジュールを提示した。初動対応から改善が見られ、生産数増加後もトラブルなく稼働。不具合時と比較して3倍程度の処理能力に。
一連の課題解決力・技術力が信頼され、リピートに繋がっている。